Polyimide wrapped wires are the optimal choice for modern powertrains, where performance beyond common expectations is required.
The transition to electric mobility is in full swing, and marks the step towards the abatement of greenhouse gas emissions. There are many investments underway in e-mobility. After all, the electric car is nothing new, indeed, it was born before internal combustion cars.
Apparently, nothing seems simpler: just replace the heat engine with an electric one, mount the battery and that’s it: right? Not exactly.
First you have to optimize, reduce weight and costs. More efficient motor means compact design; and compact design means more stress on the components.
Our flat wires wrapped in polyimide are the right choice for the challenges of the modern powertrains!
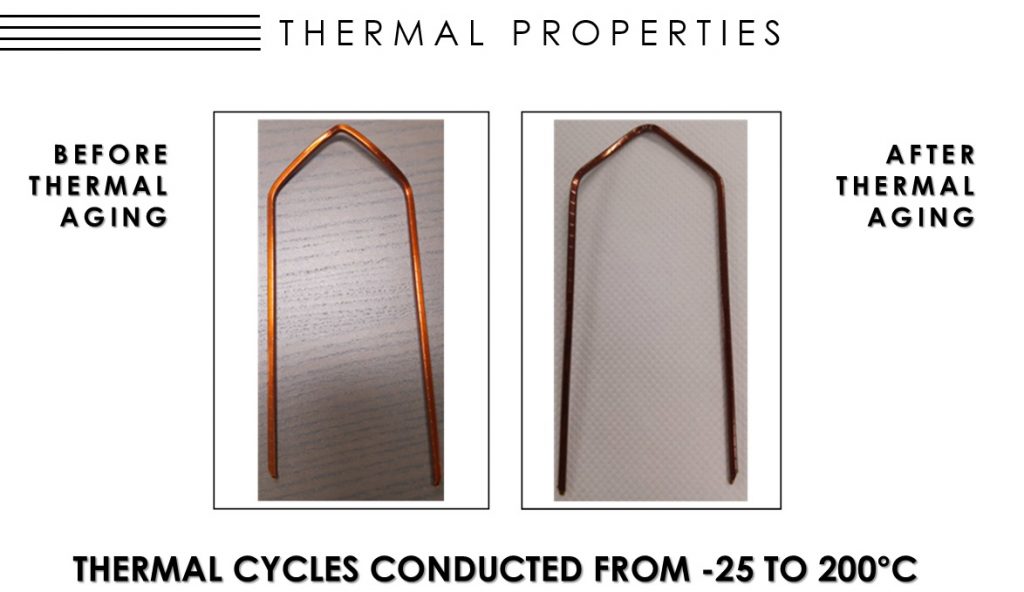
The standard enamelled wires, used for the windings, were born and raised in the shadow of industrial electric motors: however, the powertrain requirements are different. Some of the challenges are, for example:
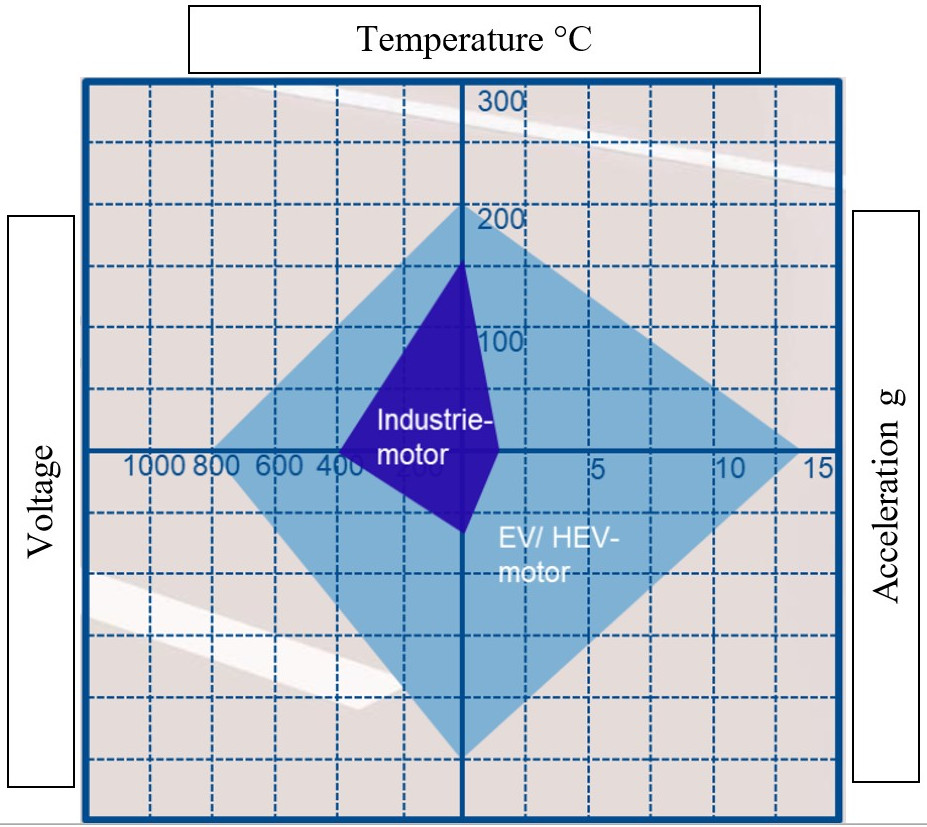
- The operating voltages, ranging up to 800 V (but will grow over 1kV in the future), coupled with electronic inverters working at frequencies up to 50 kHz, which significantly vary the waveforms. Higher voltages and frequencies bring to the generation of partial discharges, enemy of organic components such as wire enamels, which tend to degrade rapidly over time.
- Operating temperatures constantly close to 180-200 °C, with peaks of up to 250 °C are the direct consequence of compact design and narrow installation spaces. In some cases advanced cooling systems are required, such as immersion of the winding in ATF (automatic transmission fluid) liquids or oils, particularly aggressive for traditional insulating enamels.
- Mechanical properties: punctual accelerations over 10g, high filling factors and automation of winding construction processes require conductors with special shapes, capable of withstanding particularly heavy forming and mechanical bending processes.
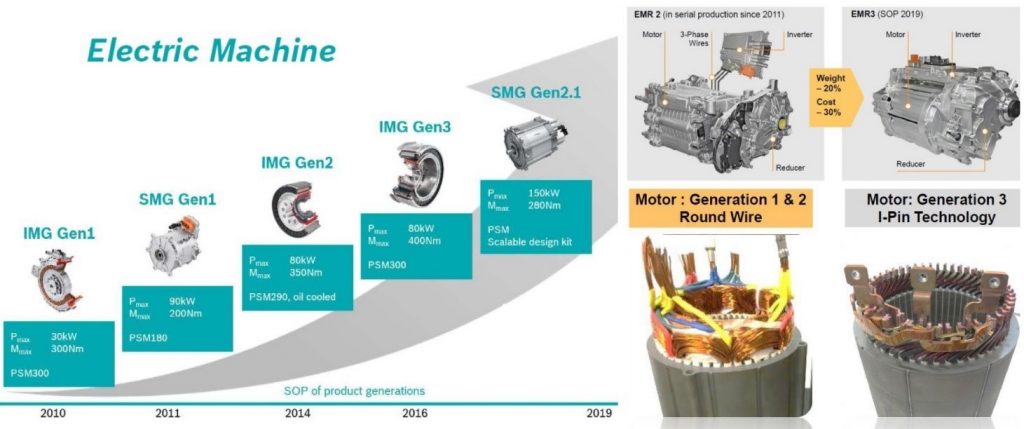
It is not easy to satisfy all these requests with just one product. In fact, the market offers various solutions, among which the most famous are:
- The co-extrusion of high performance techno-polymers (e.g. PEEK), with excellent technical characteristics but high, if not prohibitive, costs;
- The application of quantities of enamel much higher than the standards: this helps to improve the electrical properties but poorer results on the surface smoothness and flexibility of the insulation.
In this context, polyimide tapes are an excellent alternative because they have the benefits of the previous solutions without burdening excessively on costs. Suitable for hairpin forming, the polyimide resists bending and twisting in an excellent way; it is also perfectly compatible with modern impregnating resins and ATF oils.
Its thermal class allows it an excellent resistance to high temperatures and to the most severe cycles of use, also suitable for the most extreme cases. Polyimide helps to get higher inception voltages for partial discharges (PDIV), with relatively low insulating thicknesses, making the motor exempt from them.
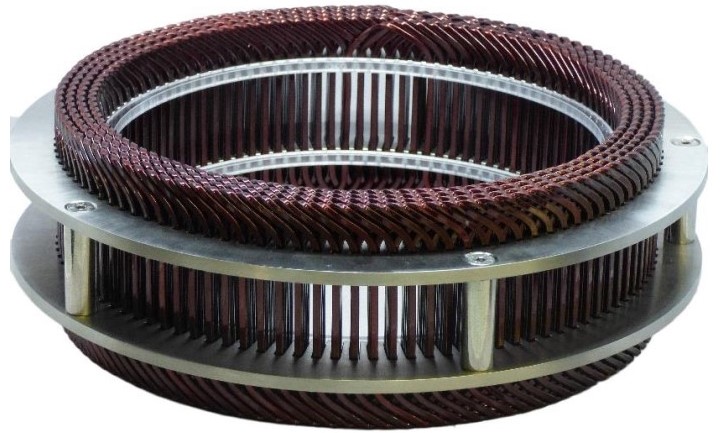
Last-but-not least, the overall cost of this solution is considerably contained compared to co-extruded techno-polymers. In addition, our brand new laboratory and testing equipment allows you to simulate the heaviest uses and ensure the quality of the insulation system.
Get in touch: our technical team will support and inspire you in choosing the right solution for your electric mobility projects.