Le piattine nastrate in polimmide rappresentano la scelta ottimale per i powertrain moderni, dove si richiedono performance oltre le comuni aspettative.
La transizione verso la mobilità elettrica è in pieno corso, e segna il passo verso l’abbattimento delle emissioni di gas serra. Molti sono gli investimenti in corso nell’e-Mobility. In fondo l’auto elettrica non è una novità, anzi, nacque prima delle vetture a combustione interna.
A quanto pare, nulla sembra più semplice: basta sostituire il motore termico con uno elettrico, montare la batteria e il gioco è fatto: giusto? Non proprio.
Prima bisogna ottimizzare, ridurre pesi e costi. Motore più efficiente significa design compatto; design compatto significa più sollecitazioni dei componenti.
Le nostre piattine nastrate in polimmide rappresentano la scelta ottimale per i powertrain moderni.
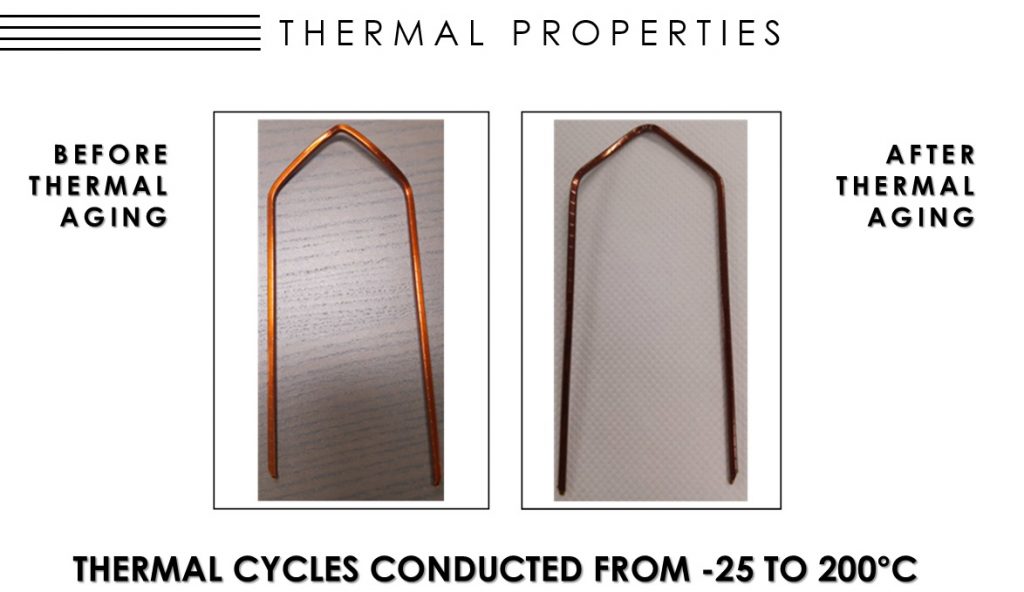
I fili smaltati standard, usati per gli avvolgimenti, sono nati e cresciuti all’ombra dei motori industriali: le richieste powertrain sono però differenti. Alcune delle sfide sono, ad esempio:
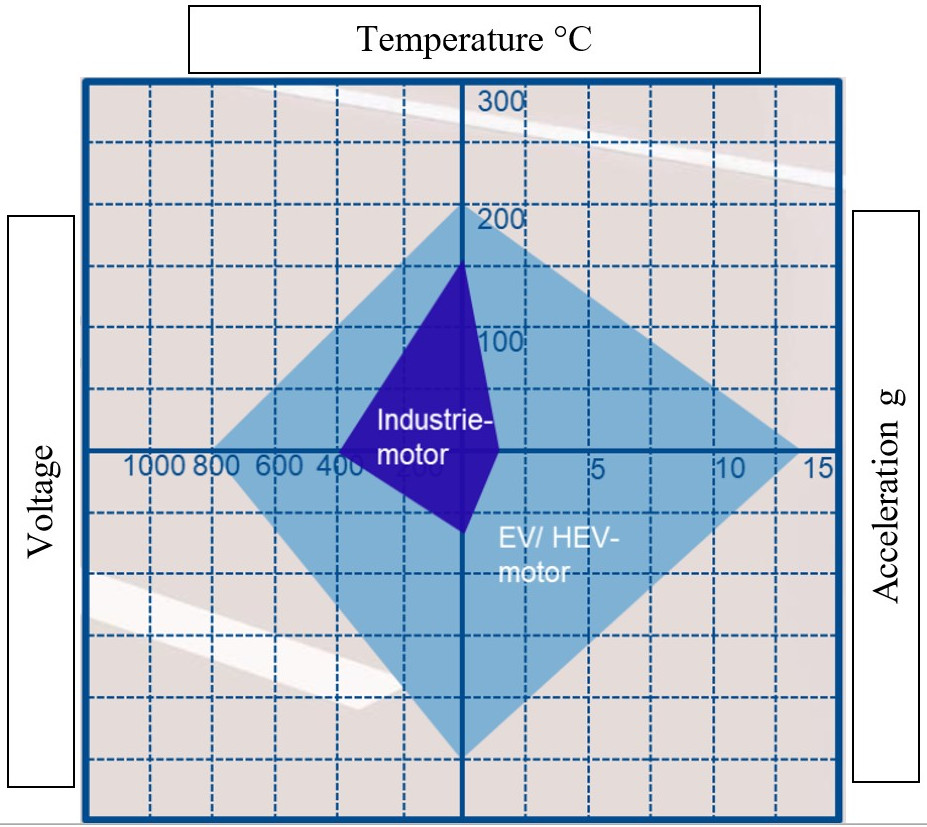
- Le tensioni di funzionamento, che vanno fino a 800 V (ma cresceranno oltre 1kV in futuro), con utilizzo di inverter e frequenze fino a 50 kHz, che variano sensibilmente le forme d’onda. Tensioni e frequenze più alte significano scariche parziali, nemiche dei componenti organici come gli smalti, che tendono a degradarsi rapidamente nel tempo.
- Design compatto e spazi d’installazione angusti, che portano le temperature d’esercizio costantemente a ridosso dei 180-200°C, con picchi fino a 250°C. In alcuni casi si ricorre a sistemi di raffreddamento evoluti, come l’immersione dell’avvolgimento in liquidi od oli ATF (automatic transmission fluid), particolarmente aggressivi per gli smalti isolanti tradizionali.
- Proprietà meccaniche: accelerazioni puntuali oltre 10g, alti fattori di riempimento e automazione dei processi di costruzione dell’avvolgimento richiedono conduttori con forme speciali, capaci di sopportare processi di formatura e piega meccanica particolarmente gravosi.
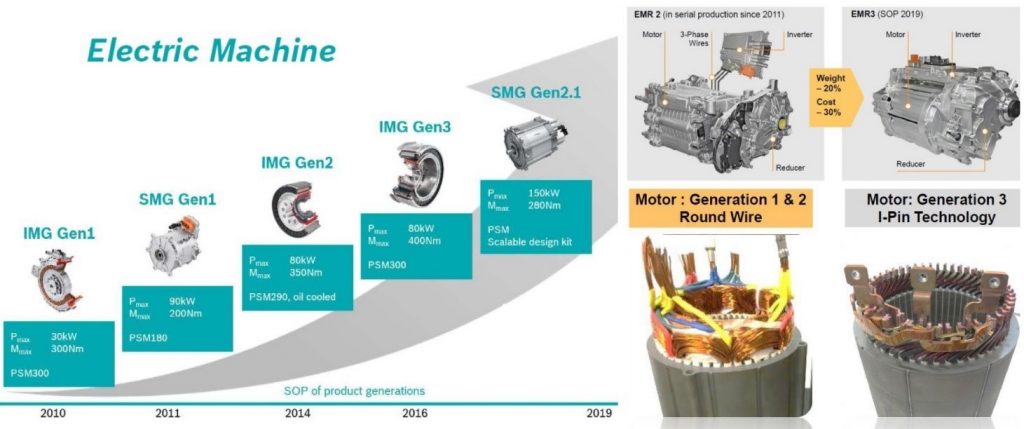
Non è facile soddisfare tutte queste richieste con un solo prodotto. Il mercato offre infatti diverse soluzioni, tra cui le più celebri sono:
- la coestrusione di tecnopolimeri ad alte prestazioni (es. PEEK), con ottime caratteristiche tecniche ma costi elevati, se non proibitivi;
- l’applicazione di quantità di smalto molto superiori agli standard: ciò aiuta a migliorare le proprietà elettriche ma porta con sé difficoltà di applicazione e flessibilità dell’isolante.
In questo contesto i nastri in polimmide sono un’ottima alternativa perché hanno i benefici delle soluzioni precedenti senza gravare eccessivamente sui costi. Adatto per la formatura di hairpin, il polimmide resiste a pieghe e torsioni in modo eccellente; è inoltre perfettamente compatibile con le moderne resine impregnanti e oli ATF. La sua classe termica gli consente un’ottima resistenza alle alte temperature e ai cicli di utilizzo più severi, adatti anche agli utilizzi più estremi. Le tensioni di innesco delle scariche parziali (PDIV) sono elevate anche con spessori isolanti relativamente bassi, di conseguenza assenti.
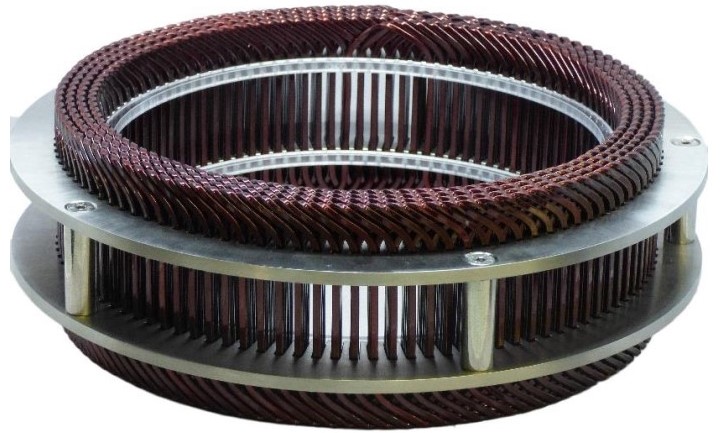
Il costo di questa soluzione è sensibilmente contenuto rispetto ai tecnopolimeri coestrusi. Inoltre, le nostre nuovissime apparecchiature di laboratorio e collaudo, consentono di simulare gli usi più gravosi e garantire la qualità del sistema d’isolamento.
Mettiti in contatto: il nostro team tecnico ti supporterà e ti ispirerà nella scelta della soluzione giusta per i tuoi progetti di mobilità elettrica.